Our Products
Shell & Tube Heat Exchangers
The company has concentrated over the years on the development of Tubular Exchanger manufacturing that enabling the focus of her extensive engineering and facilities toward the production of these equipment for the upper end market such as Refinery, Chemical, Petrochemical, Oil/Gas, Offshore and Pharmaceutical industries.
The company has also ventured & gathered extensive fabricating and welding experiences in handling special alloy material such as Hastalloy C276, Alloy 20, Alloy 200, Super Duplex , Monel, Incoloy, CrMo, Titanium, and cladding materials.
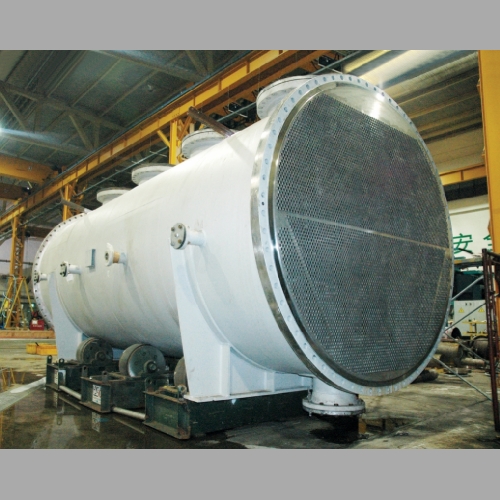
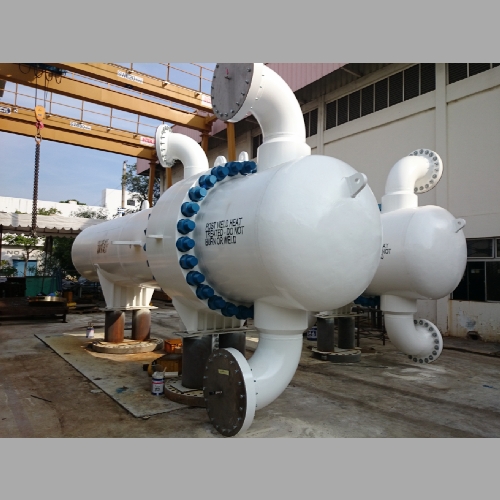
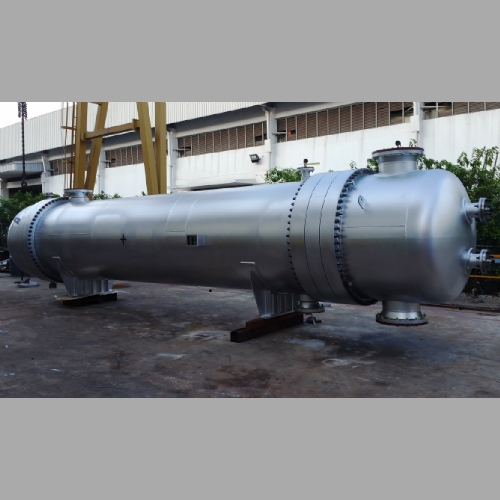
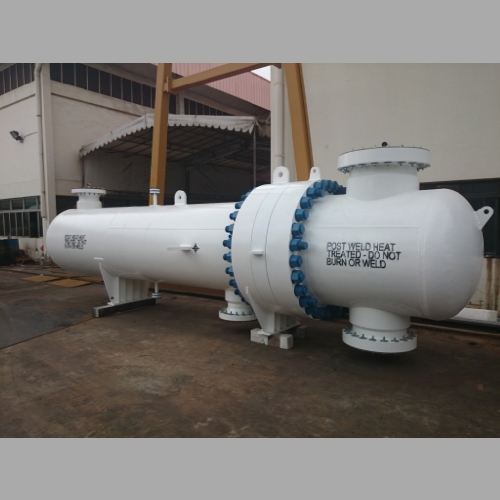
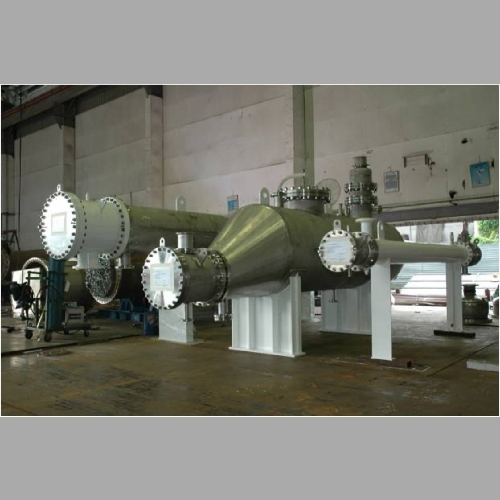
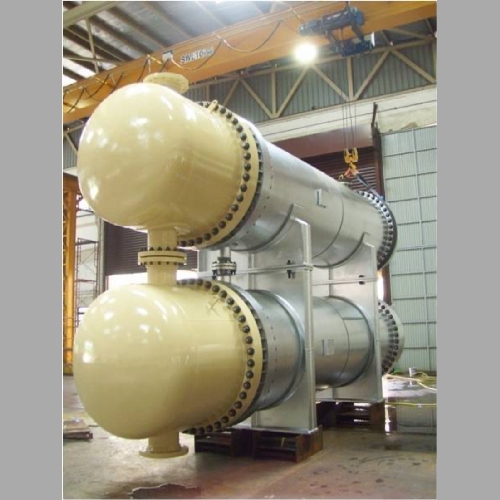
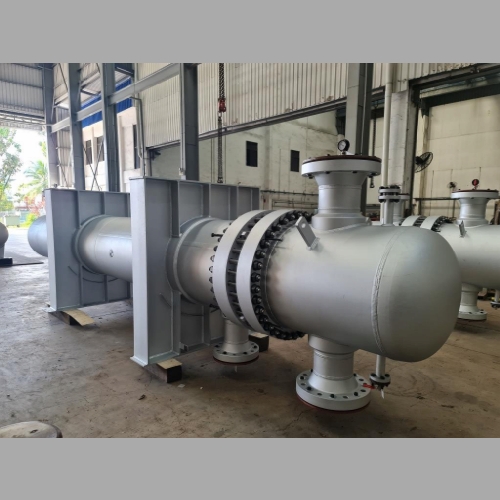
Tube Bundles & Parts
The in-house bending facilities enable us to construct U-tube bundle at the most competitive cost and fastest delivery. ‘U’ bundle is constructed in accordance with ASME VIII DIV I and API 660 requirements.
‘U’ tube bending is specified in accordance with TEMA. For bending radius not less than 2x tube outside diameter, the followings apply:
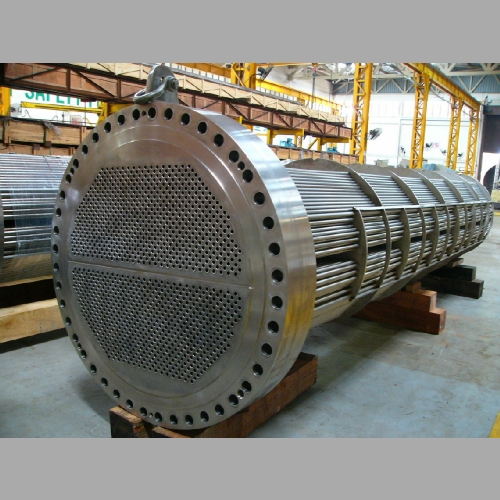
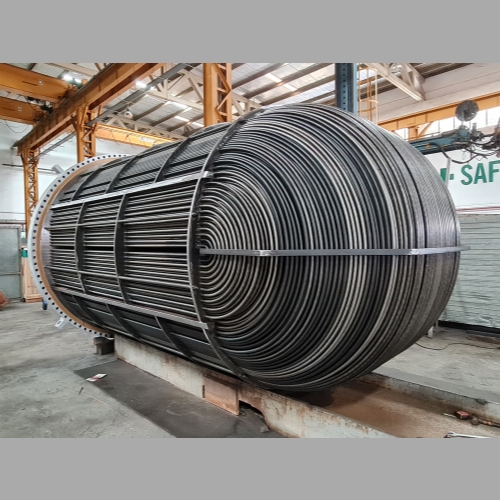
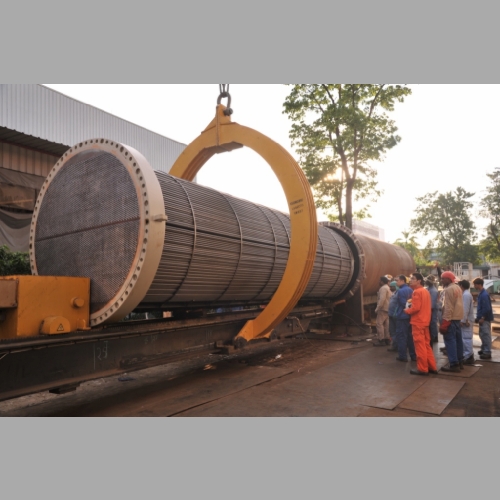
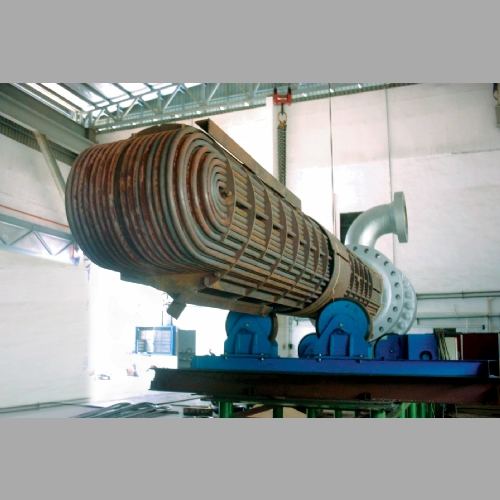
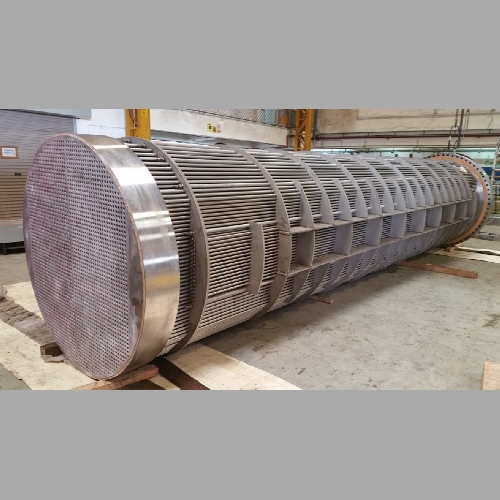
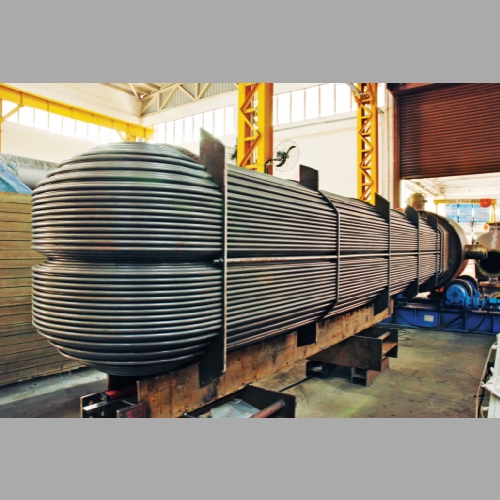
Hairpin & Double Pipe Exchangers
Our in-house modular design package for Hairpin heat exchangers in either Double pipe or Multi-tube configuration is able to arrange individual hairpin section in proper series, parallel, series – parallel combination in order to achieve the ultimate duty.
We are able to perform thermal design rating for both new and replacement exchangers. Our design construction is able to meet the various code requirements and any special customers specifications.
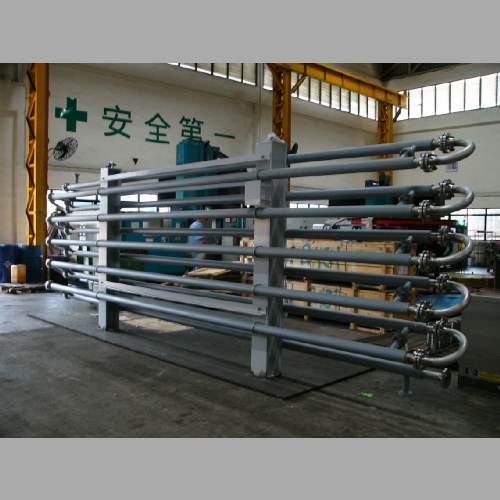
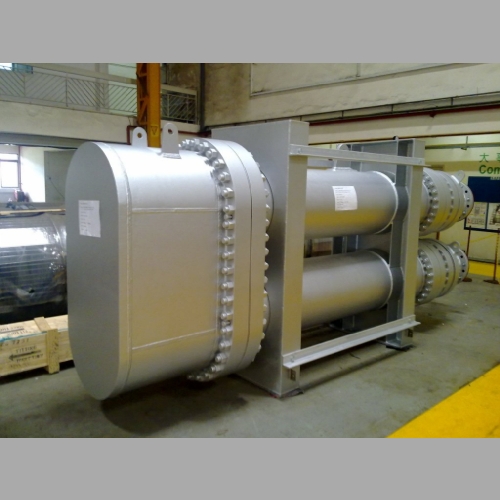
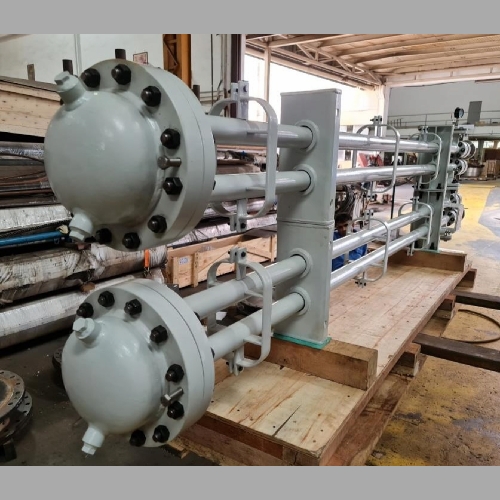
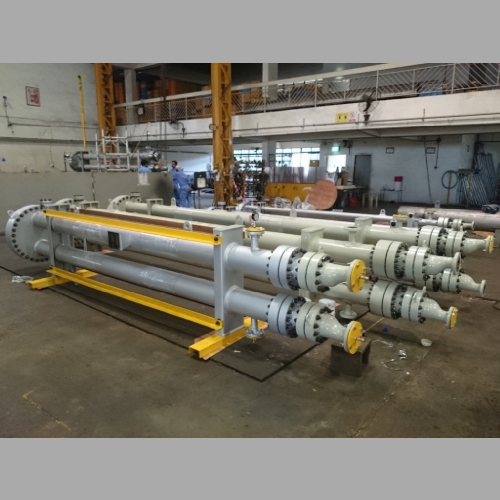

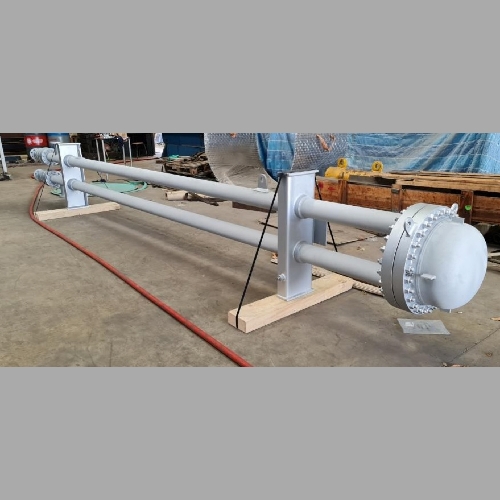
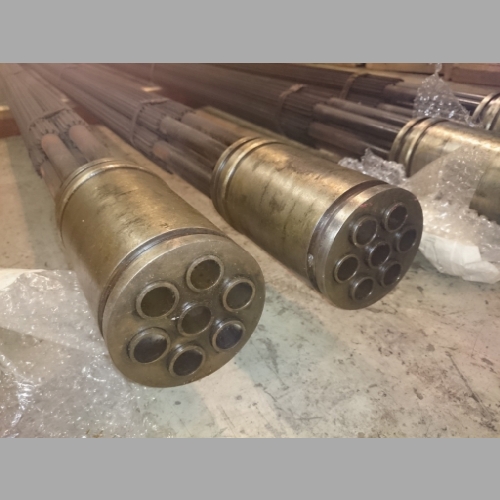
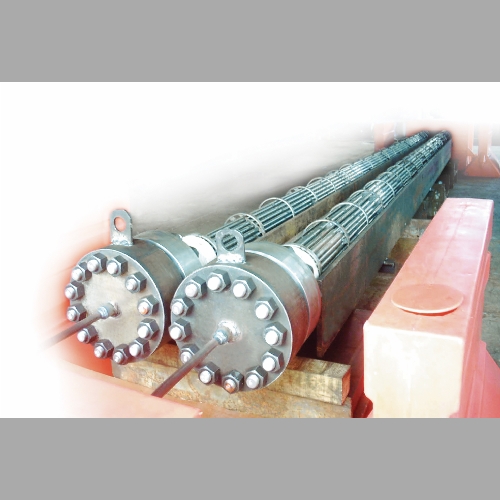
Air Cooled Heat Exchangers / Fin Fan Coolers
In addition to our expertise in traditional Tubular Heat Exchangers, Aztech Heat Exchangers has extensive experience in the design and manufacturing of Air Cooled Heat Exchangers for a variety of industries. These exchangers are essential for applications where cooling without water is required, offering efficient heat dissipation in demanding environments.
We offer a wide range of Fin Tubes to suit different design applications, ensuring that each exchanger is optimized for maximum performance.
The most common types of Fin Tubes are ‘L’, ‘LL’, ‘KL’, ‘G or Embedded’ and ‘Extrusion types
These specialized Fin Tubes allow us to tailor solutions to the specific needs of our clients, ensuring optimal heat transfer efficiency for various air-cooled applications. Whether for use in refineries, chemical plants, or other industrial sectors, our air-cooled heat exchangers deliver high-quality performance and reliability.
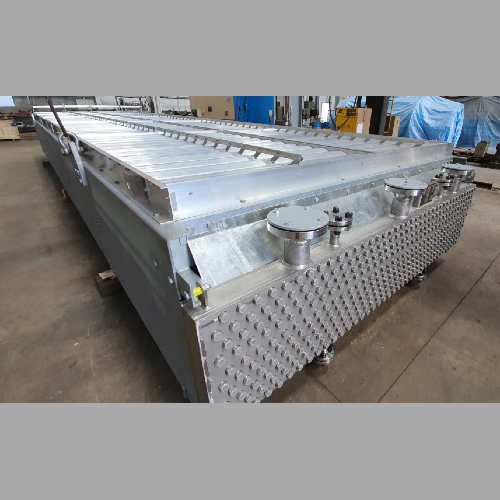
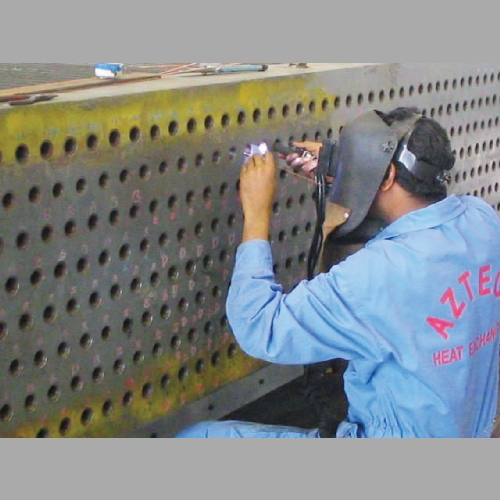
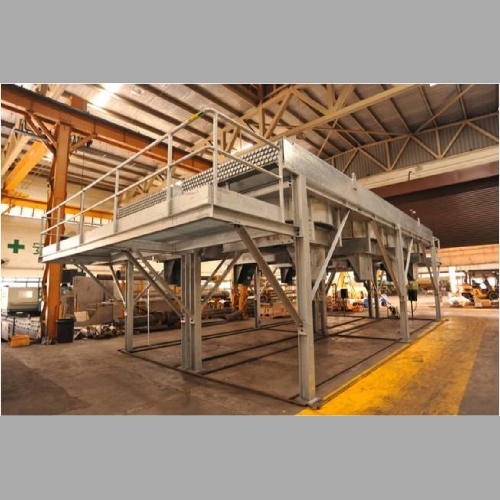
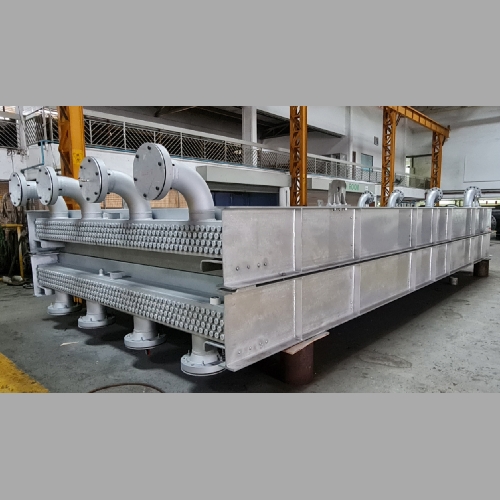
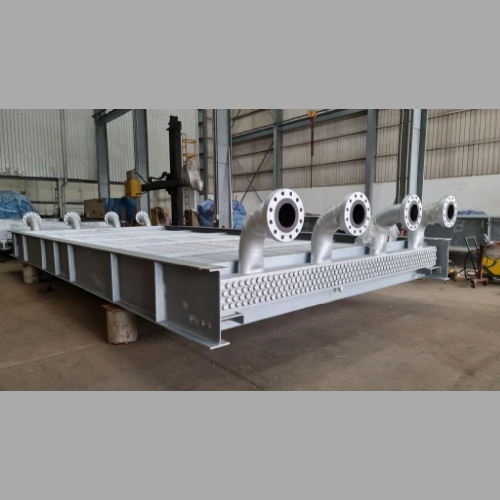
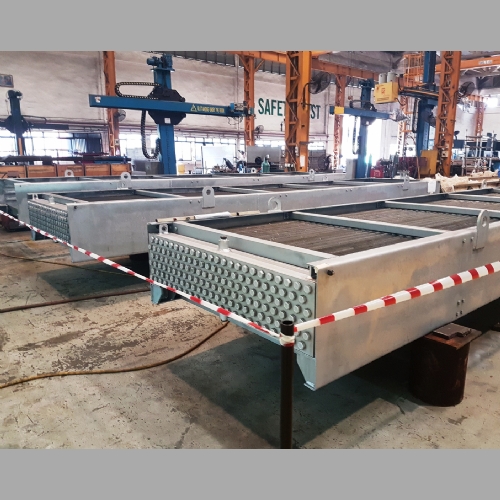
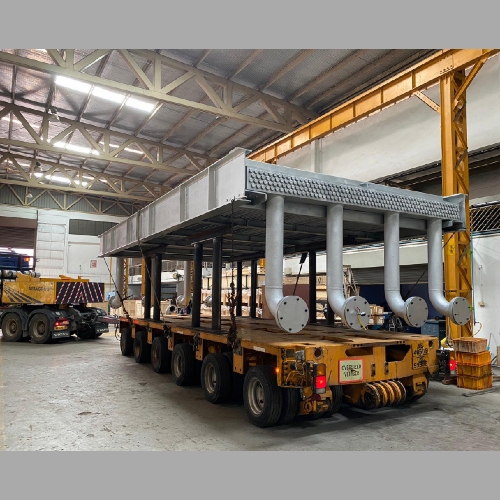
V-BANK DRY COOLERS
The V-Bank Dry Cooler is another type of Air Cooled Heat Exchanger. This air-cooler with high energy- efficiency is specially designed for industrial and commercial cooling applications especially in the Virtual Currency & Data Centres etc.
It effectively dissipates heat from process fluids by means of ambient air which also reduces water consumption and require lower maintenance as compared to the traditional cooling systems.
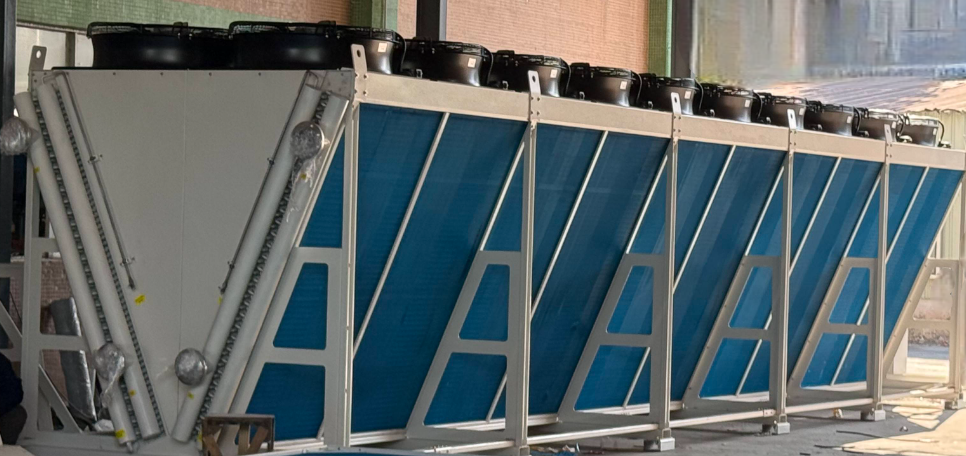
Block Fin Coolers
“AZ-FIN” designs are generated from great vast of experience and careful study of flow geometric pattern. The special louver opening created excellence turbulence and eliminate laminar flow. This high quality block fins have advantages for higher heat transfer efficiency, lower pressure drop, increase airflow rate, stronger fin to tube bonding and lesser induce vibration.
“AZ-FIN” can also use together with wireloop tube insert to further improve heat transfer performances for applications in air-air, air-oil and air-high viscous fluid.
Manufacturing Specification:
Tube Material: Copper Nickel 90/10, Aluminum Brass and Copper
Fin Material: Copper and Aluminum
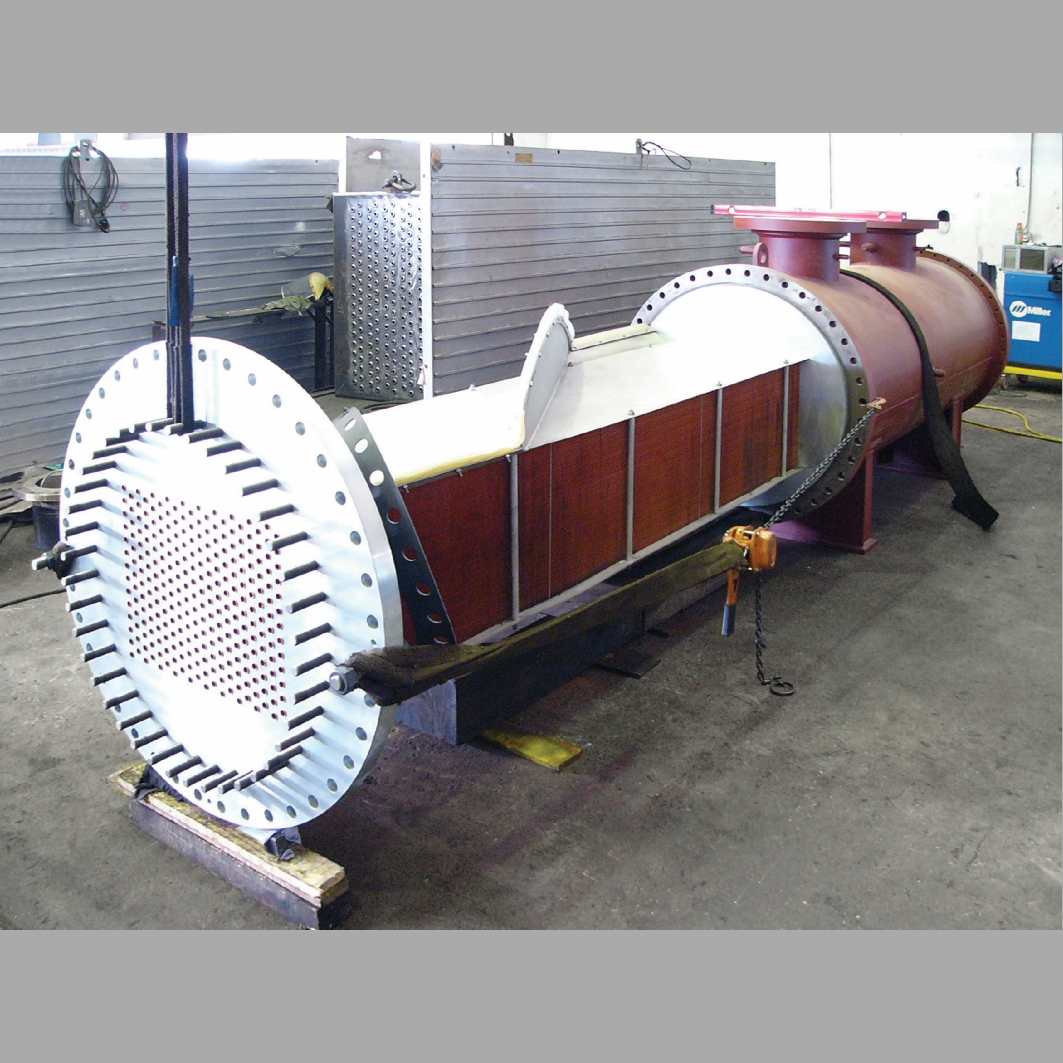
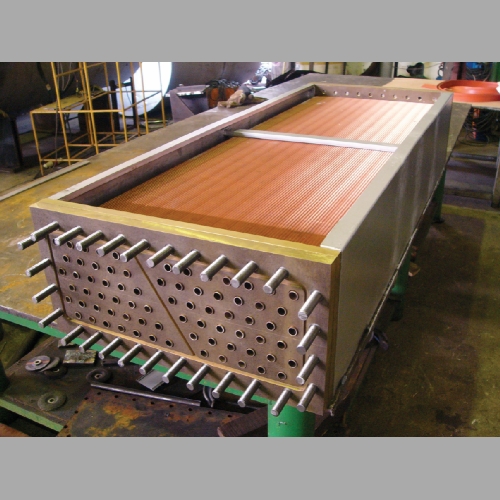
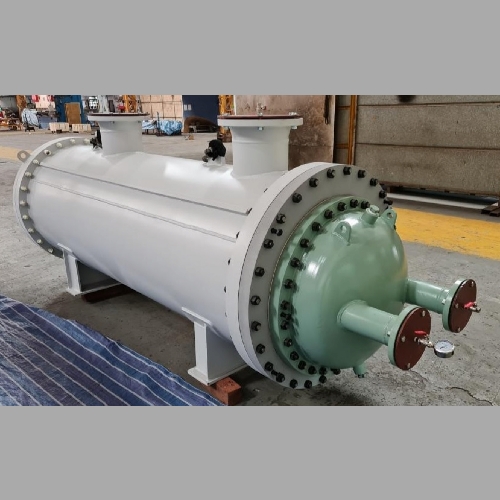
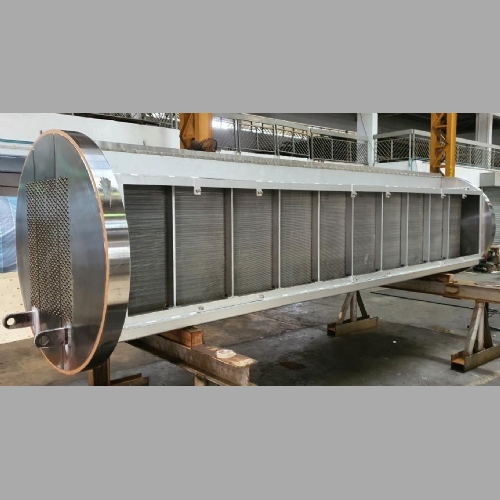
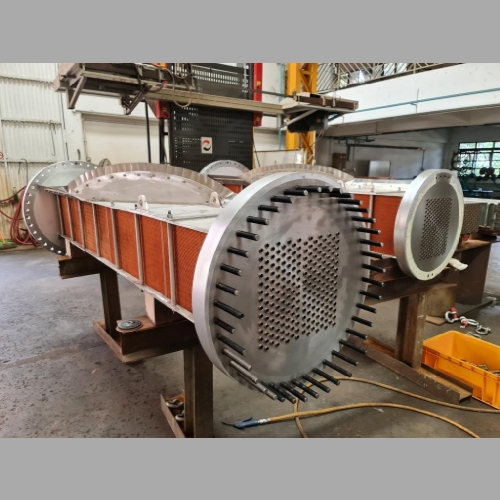
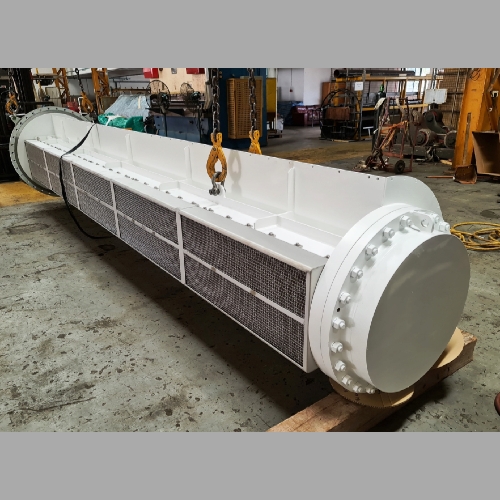
pressure vessels
At Aztech, we excel in the fabrication of pressure vessels, offering customized solutions to meet the specific requirements of our clients. Whether for storing, processing, or transporting gases and liquids, we design and manufacture vessels that are built for strength, performance, and long-term reliability.
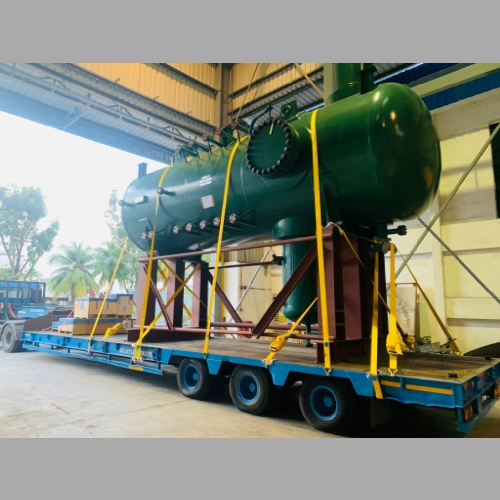
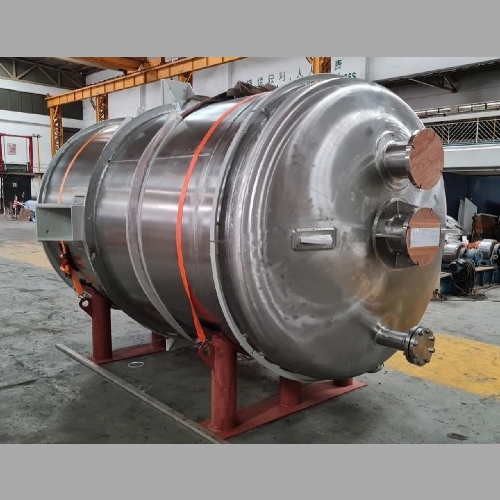
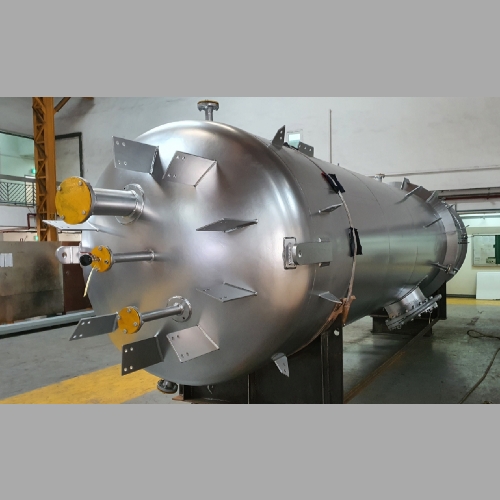
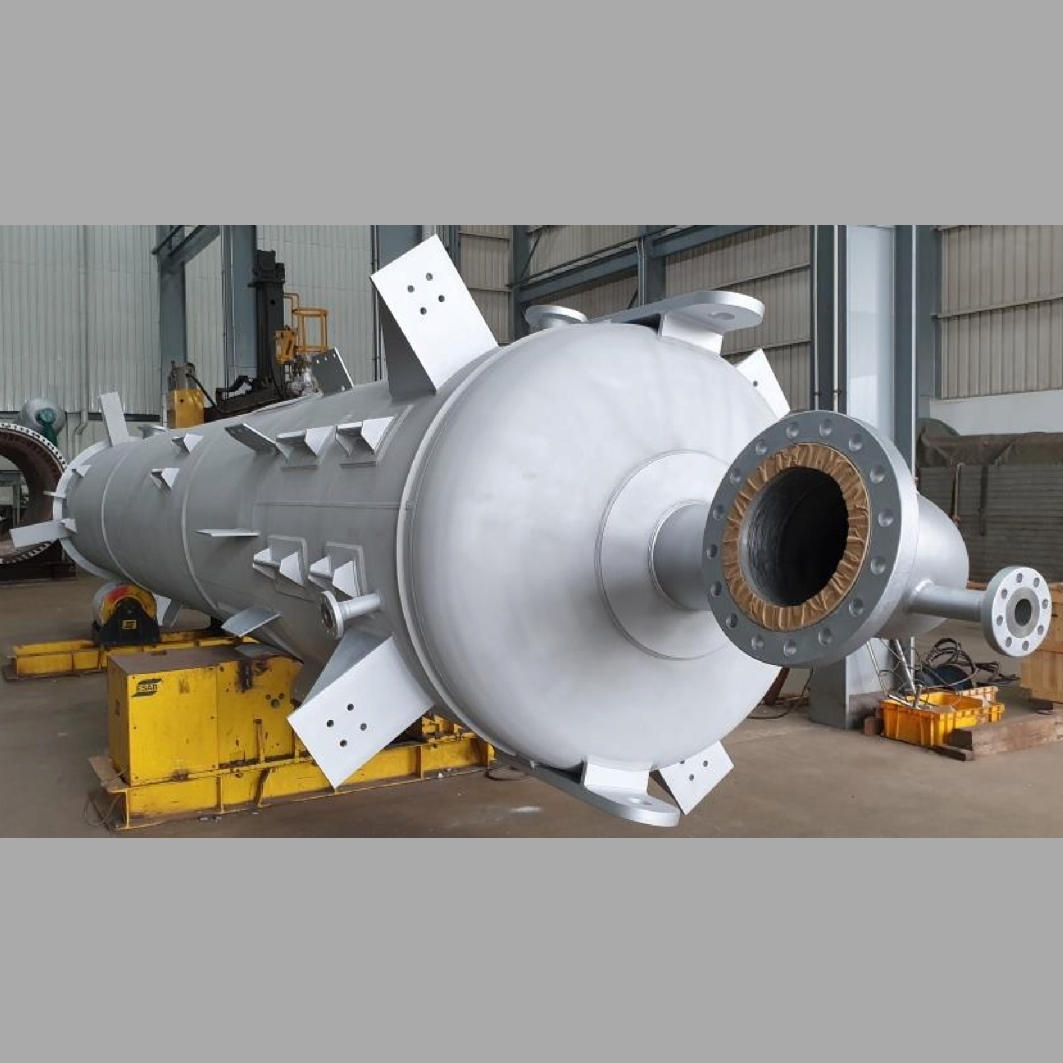
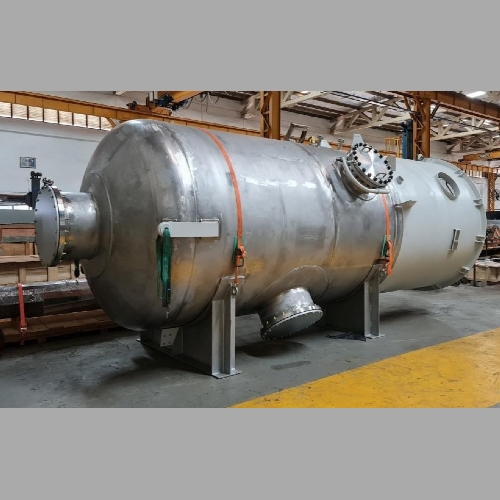
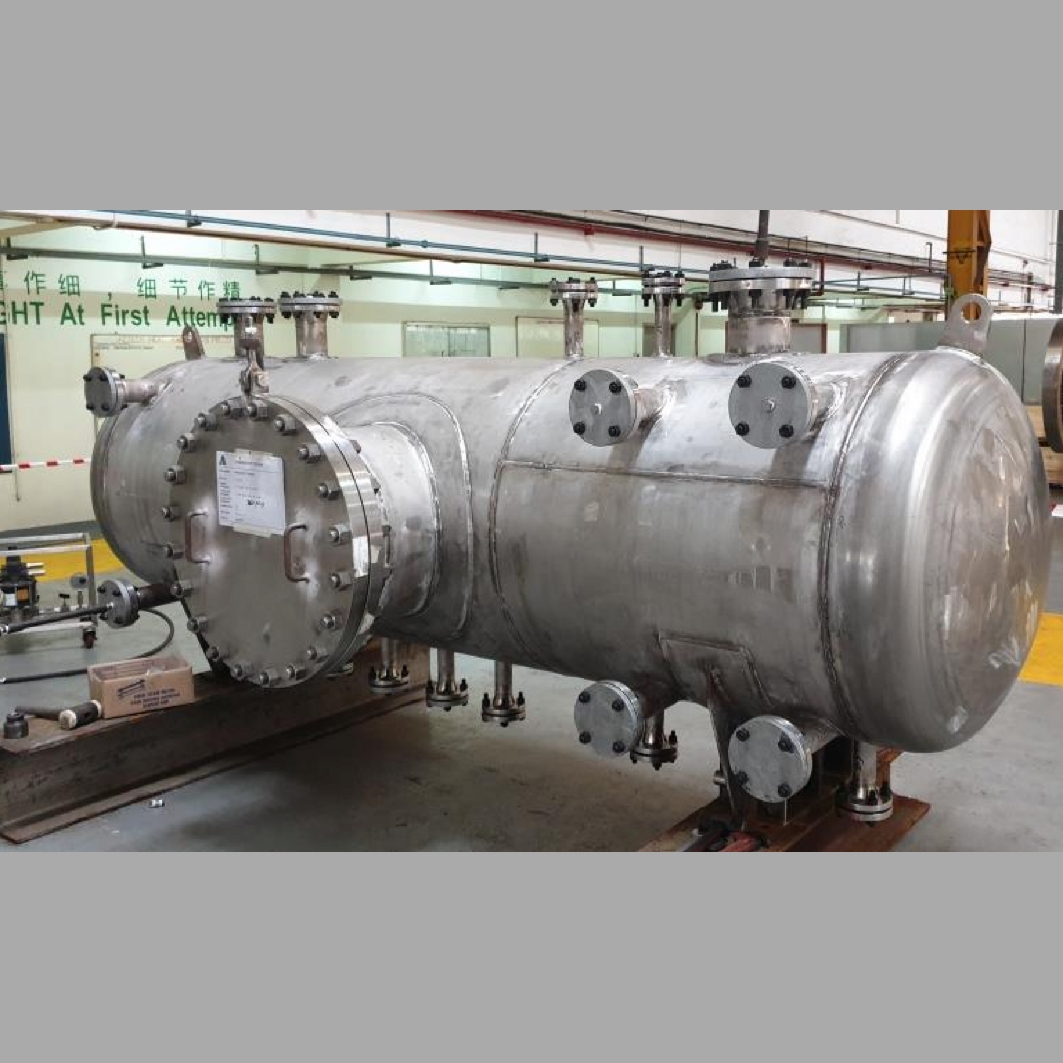
Our Partners
hiTRAN thermal systems Optimized tube-side heat transfer enhancement
Reduces size, number of bundles, weight, cost and maintenance
hiTRAN Matrix Elements are installed on the tube-side of exchangers and reactors to substantially increase the rate of heat transfer. Changing fluid dynamics from the highest velocity at the center of the tube to being highest velocity at the wall (annular type flow), increases shear and mixing, essentially removing the thermally limiting boundary layer. Fouling is also reduced as a result of lowering the wall temperature when heating and increasing wall temperature when cooling, particularly important when processing hydrocarbons.
Used in both single and 2-phase flow regimes, for new and retro-fit applications, these highly engineered systems are purpose-designed to meet specified thermal and hydraulic duties.
Applications
- Crude oil
- Residues
- Polymers
- Slurries
- Resins
- Chemicals
- Gases
- Tars
- Emulsions
- Acids
- Refrigerants
- Lube oils
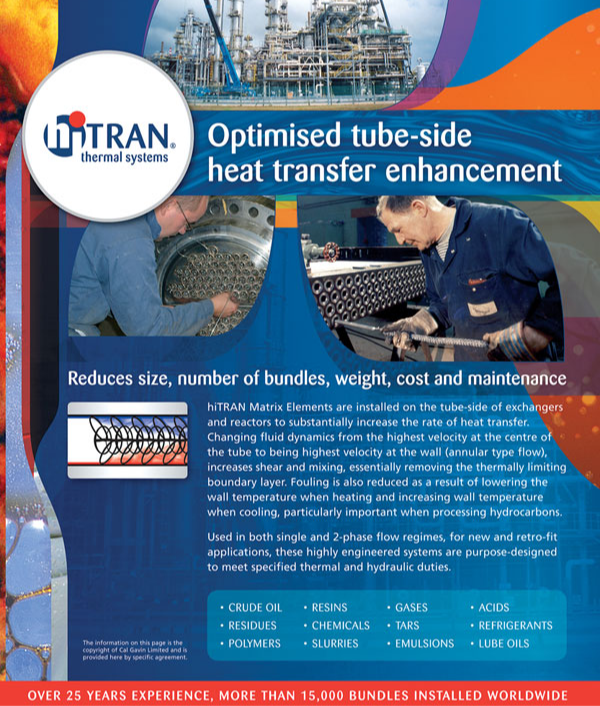
Our Partners
The HELIXCHANGER heat exchanger uses Lummus Technology’s industry proven, enhanced heat transfer technology to provide solutions for common issues such as shell-side fouling, high pressure drop and vibration. It is a particularly efficient choice for expansions or plant upgrades with lean budgets and limited plot space.
Lummus Technology experience and know-how comes from more than 3,000 HELIXCHANGER heat exchanger installations in refining, power and petrochemical
facilities worldwide. Whether the need is to extend the operating period between cleaning for a crude preheat unit, reduce capital cost in a petrochemical plant or improve energy efficiency for a feed-effluent tower, Lummus Technology’s advanced heat exchanger technology can supply the solution.
Reduces life cycle costs
An optimally designed HELIXCHANGER heat exchanger can be smaller and less expensive than a conventional segmental shell and tube heat exchanger, providing significant savings in capital costs, piping/structural costs and plot space. HELIXCHANGER technology also provides substantial savings in maintenance and operating costs for new plants and revamps of existing units. For feed-effluent applications, a HELITOWER (“Texas tower” with HELIXCHANGER bundle) can be designed at lower cost and better performance than a conventional “no tubes in window” design.
HELIXCHANGER heat exchangers are well suited for plant revamps where reuse of existing shells and piping results in significant savings in investment costs. Upgrading from conventional segmental baffles to HELIXCHANGER baffles provides increased plant capacity, while avoiding vibration problems. When vibration risk is severe, our “double helix” design is available to provide extra tube support without compromising performance.
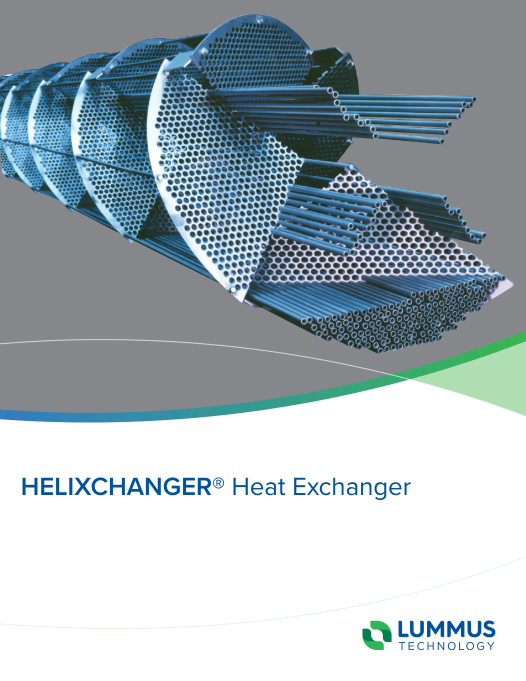
key features and benefits
Helical flow pattern
- Eliminates dead zones and recirculating areas
- Improves thermal effectiveness
Enhanced heat transfer
- Lowers capital costs
- Improves energy recovery
Better tube support
- Reduces vibration hazards
- Lowers maintenance and total life cycle costs
Shell and tube design
- Can be used within existing shell
- Available through a network of licensed fabricators